Table Of Content

Injection moulding with thin walls can produce walls as thin as 0.5mm (0.020"). Work with an experienced injection moulder and design engineer to ensure that the proper wall thicknesses are used for the design and material selection of your part. After the 3D product design, the company hired proceeds to the manufacture of prototypes. A dedicated mold is required for each component to be manufactured by injection molding.
Sharp Corners in injection molded Plastic Parts
Recommended boss wall thickness is 0.6 times of nominal wall thickness of the plastic part. Product designers design boss features in plastic parts to receive screws, threaded inserts, or guide other parts. Depending on the different types of manufacturing processes, there are set guidelines for DFM practices that define various tolerances, rules, and manufacturing checks related to DFM.
Bio/Pharma/Semi Suite Products
Upstream Innovation: a guide to packaging solutions - ellenmacarthurfoundation.org
Upstream Innovation: a guide to packaging solutions.
Posted: Wed, 18 Oct 2023 12:38:32 GMT [source]
Do you want a more accurate quotation and evaluation of your project feasibility? Please, contact us to make conceptualization, design, production, storage, and distribution easier for you. We can guide you at Martin's in answering these questions and thus reduce the production cost of your project. So, if you’re looking for the right supplier or a new one to increase your sales through attractive original plastic designs for houseware, toys, or promotional products to position your brand and impact the market, keep reading.
Shared Cost Combo Runs
This helps to make plastics more affordable than most other materials and sees them used to create millions of tonnes of single-use items every year. Our latest Dezeen guide includes more than 11 types of plastic commonly used in architecture, design and interiors, with links to hundreds of projects for inspiration. This stage is so crucial that the manufacturing cost can increase by 40% if the assembly of the product is not considered. It can also be interesting to think about what these colors and shapes were in their previous life as trash. But the important thing is that the materials and process in creating Debris is fully sustainable and it can be disposed of properly when you no longer need it. And hopefully, you get to think about what you’re doing to help preserve marine life and keep places like beaches a safe haven for all.
Unique Materials
Incorrect material specifications will lead to premature product failure, product liability, or expensive product recalls. IDS has extensive experience selecting materials based on a wide range of application requirements. Some applications require materials with excellent chemical resistance; others require exceptional impact strength, high-temperature resistance, or flame retardancy. It’s critical for your design firm to comprehensively analyze your specific application requirements and identify crucial performance requirements for the plastic material.

Guaranteed Quality
These two factors interrelate with each other, and knowledge of each area is important to achieve a comprehensive design. For plastic design, there are specific rules regarding part geometry, which supports in achieving the intended embodiment. This month's Dezeen In Depth newsletter delves into the debate surrounding the future of plastics and features an exclusive interview with interior designer Kelly Wearstler. The Plastic Design engineering team can take a product from concept to completion; this includes design, engineering, component selection, testing, and validation.
What does DFMA - Design for Manufacturing and Assembly - mean?
The purpose of using ribs is that they increase the strength of an element without increasing the thickness of its walls. With less material required, ribs will be an economical solution for added strength. For increased stiffness, increase the amount of ribs instead of increasing height and space a minimum of double the nominal wall thickness except each other.
Newsletter
Consideration of those elements is prime for integrating engineering and manufacturing expertise to catch mistakes, see opportunities for efficiencies and price reduction, and even assess the viability of contract requirements. Typically, your injection molder will conduct an in-depth analysis of those elements together with your team well before the tooling process is initiated. DFM isn't a “stand-alone” guideline or principle when it involves manufacturing plastic injection molded products.
A small radius at the boss base increases boss strength and helps in part ejection during injection molding. Simulation studies (mold flow analysis for plastic parts) can reduce the risk when the plastic part design is not following all guidelines. How features of a part are formed during a mold determines the type of draft needed.
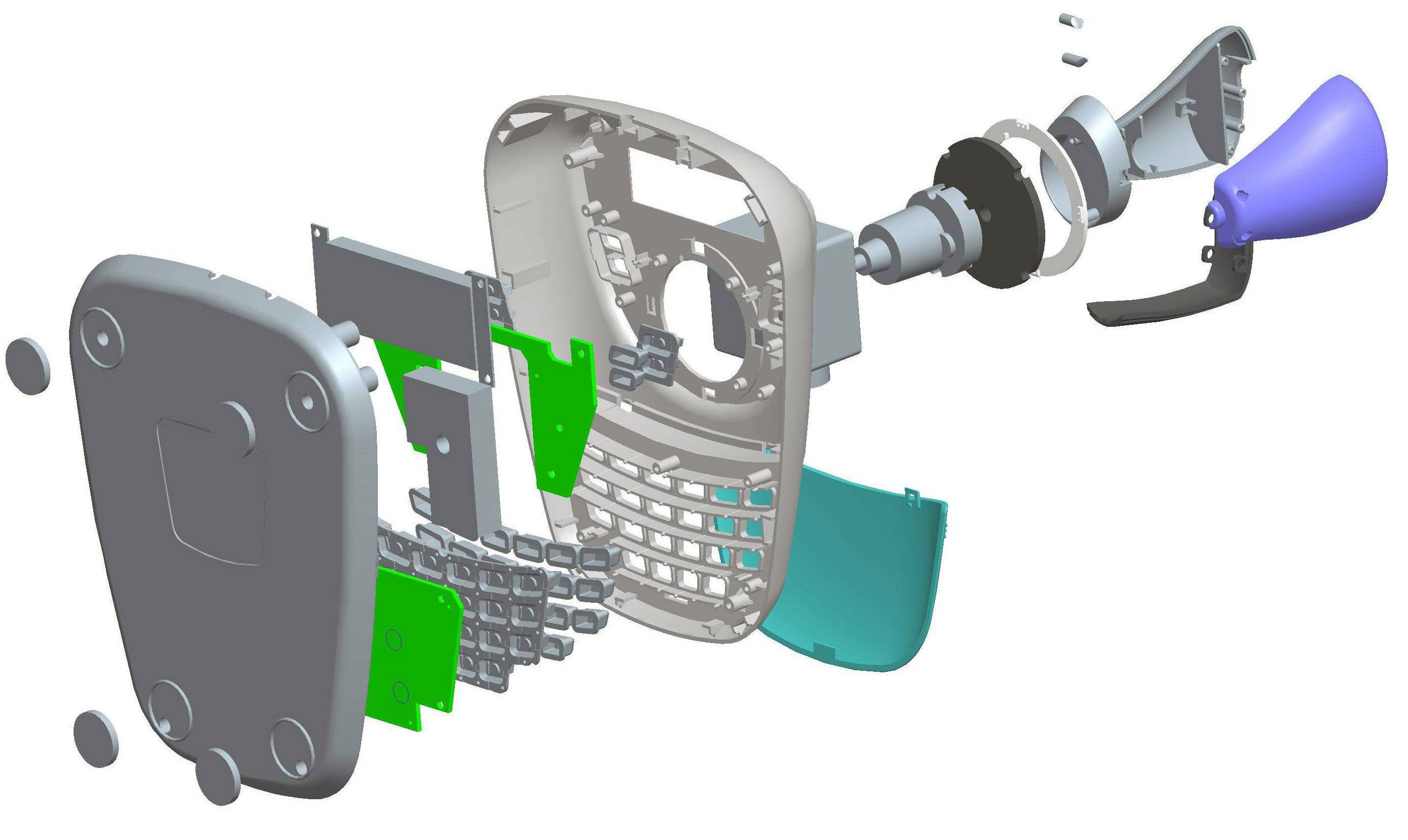
UndercutsUndercuts can be thought of as any indentation, protrusion, or hole that prohibits the injection mold from opening and ejecting the part in a linear motion. Undercuts often add significant cost to the mold as well as increased lead times. Now, the cost of manufacturing depends on the customer's business strategy and its economic potential. Still, as usual, the quote for the manufacture of a plastic design is multi-factorial.
As an innovative and eco-friendly company, Martin's proudly includes poliagave amongst its range of materials. In the junior year, you will take intermediate level courses and hands-on laboratories in polymer materials, processing and design (including the design and manufacturing of an injection mold). During your senior year, you choose among advanced courses and a student-selected capstone project.
Most bosses, ribs, and posts formed by blind holes or pockets should taper thinner as they extend into the mould. Surfaces formed by slides won't need a draft angle if the mould separates from the surface before ejection. Incorporating angles or tapers on product features like walls, ribs, posts, and managers that lie parallel to the direction of the discharge from the mold can ease the ejection of part. The type of draft required is determined by how the features of a part are formed in a mould. If the mould separates from the surface before ejection, surfaces formed by slides may not require a draft. Consider incorporating draft angles on product features such as walls, ribs, posts, and bosses that run along the direction of release from the mould, thereby facilitating part ejection.
No comments:
Post a Comment